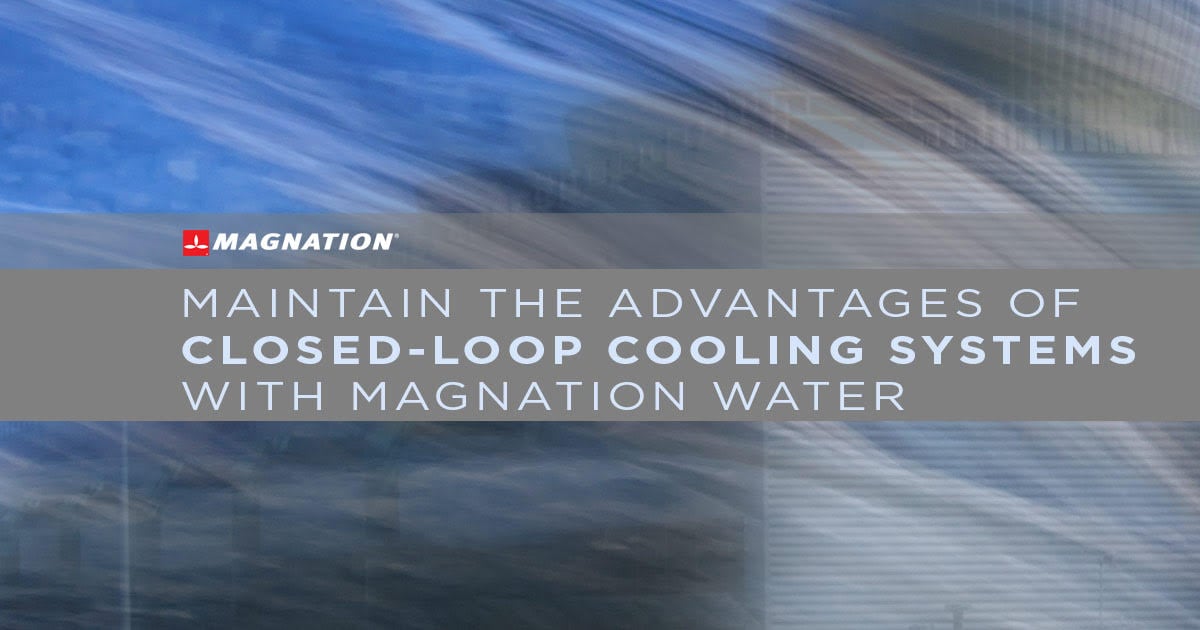
Power plant cooling water systems, facility environmental control systems, petrochemical plant cooling systems, and other industrial HVACR applications—often utilize closed-loop cooling systems. The systems offer the advantages of energy efficiency and low-maintenance costs. As an example of the industrial uses for closed-loop cooling systems, a power plant may depend on multiple closed-loop cooling systems to consistently maintain the correct temperatures of critical components such as pump bearings. For processing plants and manufacturing plants, closed-loop cooling towers use evaporative cooling to transfer heat energy into the atmosphere. In food processing and pharmaceutical applications, closed-loop chilled water systems supply the cooled water that allows air chillers to exchange heat within a larger cooling system.
Closed-Loop Cooling System Operation
In contrast with open cooling systems, closed-loop cooling systems do not allow contact between the atmosphere and the process cooling water. The carbon-steel tubing that carries cooling water remains closed.
Closed-loop cooling systems used for oil refineries, large chemical processing plants, and other high-pressure operations often rely on tube and shell heat exchangers. This approach uses two fluid circuits placed inside a large pressure vessel. One circuit overlays on the other with the fluid in the first circuit recirculating on the outside of the second circuit. As hot water flows through the tubing that makes up the second circuit, heat transfers from one fluid circuit to the other. Air drawn through the system establishes evaporative cooling.
Tube and shell heat exchangers work for more applications at lower costs. The lesser-used plate and frame heat exchangers accomplish heat transfer over large areas and support for low-and medium-pressure HVACR applications. A basic plate and frame heat exchanger consists of a series of alternately stacked cold and hot water corrugated plates placed on a frame. Hot fluids travel down plates designated for heat and counter currently to cold fluids flowing up through plates designated for cold. While the fluids do not mix, the restricted flow of water flowing through narrow channels causes turbulence, and pressure loss to increase. Heat transfer occurs from hot water to cold water through the plates.
Corrosion Can Occur in Closed-Loop Cooling Systems
Closed-loop cooling systems may appear to operate normally for long periods of time. Completely enclosing the cooling water reduces opportunities for contamination. However, controlling the chemistry of the process water is essential for optimal performance of the system. Preventing corrosion from harming carbon steel tubing requires maintaining an alkaline pH environment. Decreased pH levels may indicate that bacteria have begun to grow within the system, or that a leak exists.
Several other factors can lead to deteriorating performance. Changes in pressure allow the buildup of calcium carbonate, calcium sulfate, strontium sulfate, barium sulfate, silica, silicates, and concentrations of minerals that exceed the solubility of water. The decrease in solubility allows alkaline, non-alkaline, and silica-based scale to form on surfaces that contact water. As the accumulation of calcium and magnesium minerals increases, the water has a higher density than pure water, sinks to the bottom, and becomes more stationary. Stagnant water in a closed-loop cooling system encourages corrosion.
Incremental changes in the pH and alkalinity of cooling water can increase calcium carbonate precipitation and promote corrosion. Other factors that produce corrosion include galvanic reactions between the copper, iron, brass, and aluminum fittings, changes in temperature, and irregularities in tubing surfaces. Any exposure to atmospheric oxygen increases opportunities for corrosion.
Calcium carbonate precipitation causes deposits to increase on the surface area of tubing. The oxygen content beneath the deposit falls below the oxygen content of the process cooling water. With the difference in oxygen content for each area, the area below the deposit forms the starting point of corrosion—a stationary anode. Water flowing at a reduced velocity above the deposit allows the area to form a stationary cathode. The difference in electrical potential between the anode and cathode allows current to flow.
The presence of chloride ions increases the corrosivity of the area and allows a pit to form. Increased corrosion in the pit produces an excess of positively charged metal cations that attract negatively charged chloride anions. Increases in the amount of corrosion and the rate of corrosion cause pitting to increase and produce small leaks.
Biofilms May Exist in Closed-Loop Cooling Systems
Even in a closed-loop system, the potential for microbial growth and corrosion exists. As an example, maintenance teams add makeup water to compensate for water losses that occur during repairs on valves, pumps, and controls. The makeup water may contain dissolved minerals and oxygen that promote the growth of mineral scale, corrosion, and microorganisms.
Untreated water in closed-loop cooling systems can serve as an optimal growth environment for biofilms. In addition, small changes in temperature can prompt biofilm growth. Microorganisms in cooling water can form biofilms on the inside surface of tubing and prompt microbiological-induced corrosion. The biofilms may consist of strictly aerobic bacteria or anaerobic bacteria. Aerobic bacteria develop in aerated sections of a system. If the water flow decreases, the bacteria reduce the amount of oxygen in the water.
Since the organisms in biofilm consume oxygen, the base of the biofilm can cause corrosion at the base metal of tubing. The by-products of microbial growth include corrosive acids that attack metals. Anaerobic bacteria thrive near tubing walls. Growth of the bacteria releases the corrosive iron sulfide that harms iron-based metals and eventually causes leaks.
When biofilm bacteria attach to equipment or piping surfaces, the bacteria release extracellular polymers that protect the organisms in the biofilm. As the bacteria continue to reproduce and release more polymers, the growth of biofilms coats heat exchange equipment and increases resistance to heat transfer. As the biofilm spreads, heat exchanger efficiency drops and energy losses increase.
Black Mud and Mill Scale Can Ruin Closed-Loop Cooling System Performance
The use of mixed metals and the limited maintenance seen with closed-loop cooling systems can lead to iron and steel corrosion. Each of those factors can cause the most common foulant—black magnetic iron oxide sludge—to deposit on heat-transfer surfaces. The fine, wet particles of black magnetic iron oxide compact into a dense mud or sludge that blocks smaller diameter tubing and coils in the cooling system.
Manufacturers apply a natural black iron oxide coating—called mill scale—to protect pipes during storage. Very fine particles of mill scale can wash from pipe surfaces during operation. Mill scale plugging restricts flow within the system and negatively impacts system efficiency.
Magnation Water Technologies Solve Closed-Loop Cooling System Problems
Magnation offers cost-effective solutions for protecting closed-loop cooling systems from problems caused by mineral scale, corrosion, biofilms, black mud, and mill scale. Attaching the Rainbolt or Turbulator devices to a closed-loop system preserves the mineral balance of water while eliminating environments that can promote biofilm growth.
Much of the solution occurs through providing the flow inducement needed to improve laminar flow and decrease friction. Depending on the application, either the Rainbolt or the Turbulator produce soft, energized water that reduces energy requirements, improves pump efficiencies, and reduces maintenance downtime.
Cutaway Drawing of the Turbulator
Magnation’s Rainbolt and Turbulator devices employ the combination of turbulence, vortexing, rifling, and geometry with magnetic resonators needed to reduce mineral scale or deposits of black mud. Applying passive magnetic and electromagnetic water conditioning causes water to gain an electrical charge and the agitation needed to break apart weakly bonded mineral clusters. Molded helical grooves and tapering inside Magnation’s products increase pressure and create the turbulent flow needed to separate water from dissolved solids.
As a result, the improved water flow carries calcium away and prevents minerals from adding to scale deposits. In addition, the application of strong magnetic fields continually reduces surface tension and eliminates energy losses caused by friction.
While the Rainbolt accommodates pipe diameters ranging from 1” to 4”, the Turbulator works with 4” to 12” diameter pipe. The Rainbolt is threaded, and the Turbulator is flanged to enable ease-of-attachment. For carbon-steel closed-loop systems, Magnation devices should install post-filtration to accomplish optimal thermal efficiency. The post-filter connection also eliminates the possibility of any materials bonding to the magnetism of the devices.
Magnation Water Technologies Rainbolt
Comments
Add Comment