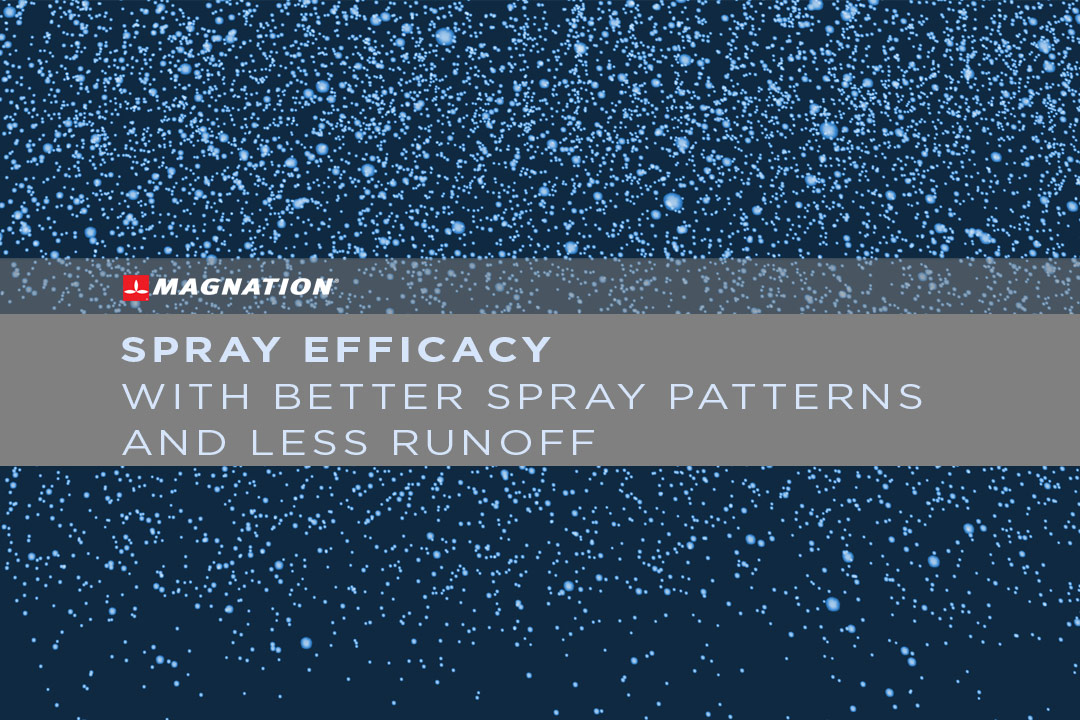
Spray irrigation offers the benefits of rainfall. While a spray irrigation system evenly distributes droplets of water on crops and grasses, landowners can control the amount of moisture according to need and the type of crop. The type and size of a system varies according to:
- Application
- Soil texture
- Water holding capacity
- Crop type
- Crop density
- Root density
- Temperature
- Water quality
Spray Irrigation Systems Match Residential, Agricultural, and Industrial Needs
The design of a spray irrigation system depends on:
- Maximum daily requirements for peak crop water use
- the desired depth of water
- the time needed for irrigation
- the frequency of irrigation
To match design requirements, spray irrigation systems rely on pumps, motors, valves, main lines and lateral pipes, risers, and perforated nozzles or sprinklers. Pumping stations located near a water source lift water under pressure for the system. Permanent or temporary main lines deliver water from the water source to the field while lateral pipes transport water to different sections of a field. Risers deliver water to sprinklers that spray pressurized water through an orifice.
The type of pumps used for a system depends on the type of application, and ranges from self-priming horizontal centrifugal pumps and jet pumps to submersible vertical turbine pumps. Irrigation systems may use electric and hydraulic control valves, check valves, pressure relief and pressure reducing valves, and foot valves. Galvanized steel, aluminum, soft plastic, Polyvinyl Chloride (PVC) and polyethylene (PE) main line and lateral pipes and hoses used for irrigation systems vary in diameter from 3 to 12 inches.
Residential landscapes and golf courses may use rotor sprinklers that pop-up from the ground or reside on the surface. The addition of jet sprinklers to a spray irrigation system adds the force needed to cover large agricultural fields. Industrial spray irrigation uses excess processed wastewater for agricultural and horticultural purposes. Each application may have different requirements for flow rate and whether the system uses surface water or well water.
Depending on the application, spray irrigation systems may deliver water to crops through low-pressure microjet nozzles, medium-pressure one-nozzle sprinklers, or high-pressure two-nozzle sprinklers. The type of nozzle and nozzle size depends on application rates, size of the wetted diameter, the desired water droplet size, terrain, and type of soil. For example, high pressures combined with small nozzle sizes combine to produce small water droplet sizes with lower flow rates that work for heavy soils and slopes.
Spray Irrigation Systems Require Clean Water for Optimal Operation
The efficiency of a spray irrigation system depends on the capability of the system to maintain pressure. However, because irrigation systems often use water from underground aquifers, the system may not maintain the pressure needed for maximum efficiency.
Brackish water flowing through an irrigation system contains calcium carbonate, magnesium, and other minerals that increase the viscosity of water and coat the inside surfaces of pumps and lateral pipes with mineral scale. As the coatings roughen the inside surfaces of pumps and pipes, friction loss occurs. Along with causing friction loss, the layers of calcium carbonate coat decrease the inside diameter of main and lateral pipes. Each of these factors cause a loss of pressure within the system and decreased water flow.
Calcium carbonate, magnesium, sodium carbonate, bicarbonate, and other mineral deposits may also clog sprinkler nozzles. As the delivery systems become blocked, the ability of the system to efficiently water established zones decreases. In addition, the corrosion caused by scale accumulation shortens the operating life of sprinklers and nozzles.
Most spray irrigation systems work best for moderate and coarse soils. However, irrigating with brackish water may harden the soil and prevent plants from absorbing water and nutrients. As dissolved minerals accumulate in soil and increase soil salinity, the soil salt binds together and creates a hardpan effect that leads to water run-off.
Magnation Water Technologies Soften Hard Water and Increase Spray Irrigation System Efficiency
Spray irrigation systems must apply water uniformly over crops. Achieving uniformity depends on maintaining the optimal water pressure throughout the system. Friction loss in pumps, pipes, and fittings causes pressure to decrease downstream and changes in pressure throughout the system.
The design of Magnation’s Rainbolt units reduces the need for irrigation by 20 percent and the energy requirements for irrigation pumps by 25 percent by conditioning hard water. Magnation products combine the effect of magnetism, centrifugal force, and vortexing to break apart mineral deposits, reduce friction, and obtain better water flow. Minimizing mineral scale through the installation of Rainbolt devices reduces spray requirements by 10 to 50 percent. As mentioned by Fred Burke of Kugler Liquid Fertilizer, the use of conditioned rain-like water for irrigation improves soil health and penetration, builds moisture retention, and extends the operating life of equipment.
Magnation’s Rainbolt
Magnation’s passive units mitigate water run-off by reducing the surface tension of water and decreasing the size of water droplets. As a result, spray irrigation systems achieve uniform distribution while requiring less pumping energy. According to Lyle Mertens of Superior, Nebraska, the installation of Magnation’s device in a spray irrigation system improved spray patterns, removed minerals that clogged nozzles, and resulted in less energy use. If you would like to learn more about how to improve the performance of spray irrigation systems, contact a water conditioning expert Magnation Water Technologies.
Comments
Add Comment